加工を極める:歯車加工
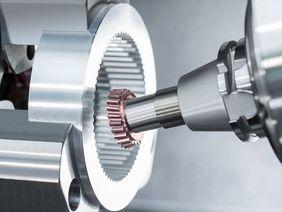
1世紀以上前、ヴィルヘルム・フォン・ピットラーは、1910年当時としては画期的なアイデアであったギヤスカイビングの特許を申請しました。しかし、ギヤスカイビング加工が現代の製造業に広く適用されるようになったのは、同期スピンドルと工程最適化ソフトウェアを備えたマシニングセンターと複合加工機が、この非常に複雑な技術の使用を可能にしたためです。ホーンの製品群には、様々な形状の歯車を加工するための工具が豊富に揃っています。外歯車、内歯車、スパーギヤ、スプライン、あるいは特殊な歯形など、これらの歯形はすべてスカイビングツールで極めて経済的に生産することが可能です。
このシステムには、内歯車、スプライン、その他のプロファイル、および干渉輪郭に近い外歯車を高い生産性で生産するためのツールが含まれています。これらの用途におけるスカイビングの最も重要な利点は、ギヤシェーパーに比べて加工時間が大幅に短縮されること、最適化された複合加工機・マシニングセンタでの使用、ワンチャッキングでの旋削と歯切り、歯先でのアンダーカットの排除です。さらに、ギヤシェーパーやブローチ盤と比較して、通常より生産的で費用対効果の高い製造工程と、キー溝加工と比較して4~5倍のサイクルタイムが短縮されることも有利な点である。このことは、歯車の歯をソリッドにハード加工する可能性にも反映されています。スカイビングツールは、中~大ロットの生産用に設計されています。各工具は、用途と加工する材料に合わせて、歯数とモジュールサイズに応じた異なる工具インターフェイスを備えています。
特に内歯車では、大型モジュールのスカイビング加工において、加工時間の短縮というメリットが得られます。大型で剛性の高い複合加工機・マシニングセンタでは、ワークと工具スピンドルの同期が必要とされます。モジュールが大きくなればなるほど、機械剛性はより重要になります。左右の側面に切削を配分することで、この問題は工具によって軽減されます。小型の超硬ソリッドスカイビングツールで経験を積んだホーンは、そのノウハウを活かして大型モジュールにも対応しました。各アプリケーションは、同社のエンジニアによって実現可能性が評価された後、工具の設計やプロセスパラメータの推奨事項に関してユーザーと議論し、その後、プロジェクトが実施されます。
例えば、航空宇宙産業のあるユーザーは外歯車の製造に約20分の時間を必要としていました。このユーザーの加工能力は限られていたため、ホーンは自社のテストセンターで何度か試験を行い、スカイビングプロセスの最適な切削パラメータを開発しました。その結果、すべてのテストシリーズで再現性があり、一貫して高い品質が得られました。スカイビングプロセスの連続生産への導入はスムーズに進み、最初のテストはすぐに成功しました。テュービンゲンで決定されたこの工程の切削データは、ほぼ一対一で転送することができました。バリ取りを行わない場合の歯車の加工時間は、20分以上から7分に短縮されました。さらに、これまで必要とされていた再加工やハンドリングにかかる時間もなくなり、同時に部品の精度も向上しました。
このシステムには、0.5から2までのモジュール用の円筒形または円錐形の工具があります。超硬ソリッドモノブロックバージョンは、直径20mmまで、スリムなデザインで提供されています。小型モジュールや小型部品の製造に使用され、衝突の危険性があるためコンパクトなシャフトが必要な場合に適しています。用途に合わせた切削材料とコーティングにより、ワークの高い表面品質を実現します。工具径が20mmを超える場合は、交換可能なヘッドシステムを備えたスカイビングツールが使用されます。精密なインターフェースにより、ホルダーを取り外すことなく、機械内でカッティングヘッドを簡単に交換することができます。超硬製ホルダーは、高い剛性、耐摩耗性、精度を保証します。より大きなモジュールの場合、ホーンはインサート交換式のスカイビングカッターを使用することにしています。特にWSRツールタイプでは、内部クーラント供給を切れ刃の前または後ろに配置するオプションがあります。これにより、用途に応じて、止まり穴、貫通穴、段付き穴の加工を最適な冷却方法で行うことができます。